How to Install and Maintain a Screw Jack System?
Screw jacks are specially-made devices designed to convert rotary motion into linear movement, making them useful for pushing, pulling, lifting and supporting loads. Furthermore, automated machinery often utilizes them to handle and manage these loads more effectively.
No matter which type of jack you select (machine/worm gear or ball screw), several factors will play a part in its proper sizing and placement, including critical speed, column strength and the type of load to support.
Lifting Capacity
Screw Jack Systems are composed of components designed to lift, position, align and support industrial loads in various settings such as packaging, maintenance lifts, material handling or space technology. They’re used in numerous applications like packaging, maintenance lifts or material handling applications – some examples being packaging.
Power is the cornerstone of a Screw Jack System’s efficiency. A higher input torque required to run a machine screw jack may make this type of system less energy-efficient than using ball screw jacks which offer less friction and superior durability.
Design of the Screw Jack System also plays an integral part in reaching its rated capacity. If not designed appropriately, damage may occur and thus reduce its rated capacity significantly.
Safety Features
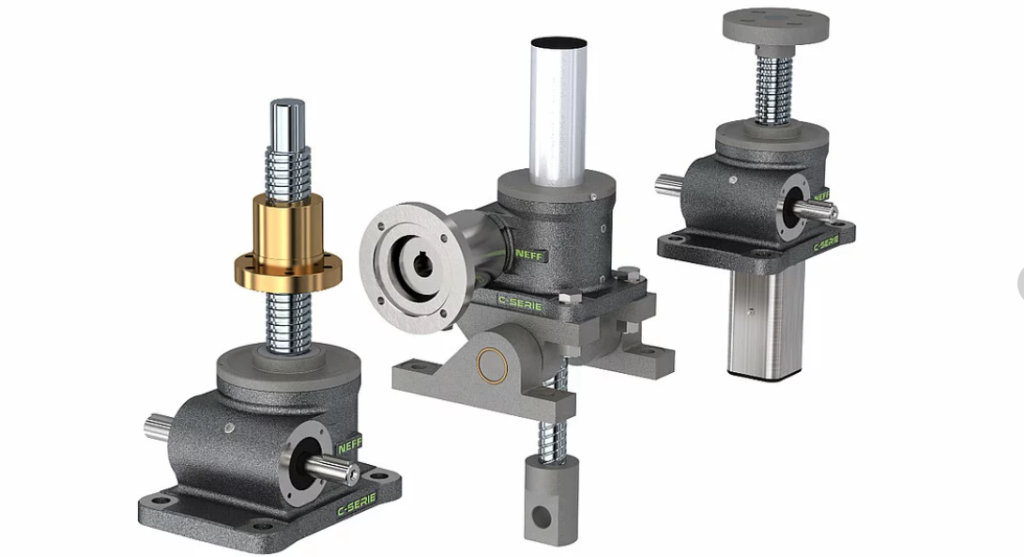
Screw jacks are widely utilized to produce controllable linear motion in many different applications. Their self-locking feature ensures that loads remain secure even if motion force is removed, making this feature especially valuable in safety-critical settings where there may be the risk of dropping loads due to failing main screw nuts.
Designing a screw jack system requires taking both thrust and guidance into account. Worm gear jacks generally only offer thrust while ball screw jacks offer both. Guide systems often prevent side load transmission but can add significant drag if not designed properly; high-lead ball screws may require larger brake motors for stopping loads if the worm gear does not feature standard brakes; shock loads must also fit within its maximum capacity of the jack.
Maintenance
Maintaining your Screw Jack System to extend its useful life is key to its survival. Depending on your application, this may involve inspecting and lubricating both its motor or gear box as well as its threaded spindle(s). Our standard NLGI Grade 2 grease that ships with our worm gear screw jacks provides a good starting point, however extra consideration must be given in saline environments which could reduce its useful life span.
To keep your Screw Jack System operating at peak condition for years to come, the most efficient method for keeping gear lubrication fresh and properly applied is replacing it at regular intervals as recommended in its operator’s manual. This should amount to replacing approximately one litre per year per jack; remembering to ensure that its temperature and pressure settings remain optimal can help maintain peak condition for years. Common issues related to lubrication include corrosion as well as loss of lube due to temperature variations or foreign matter such as dirt.
Installation
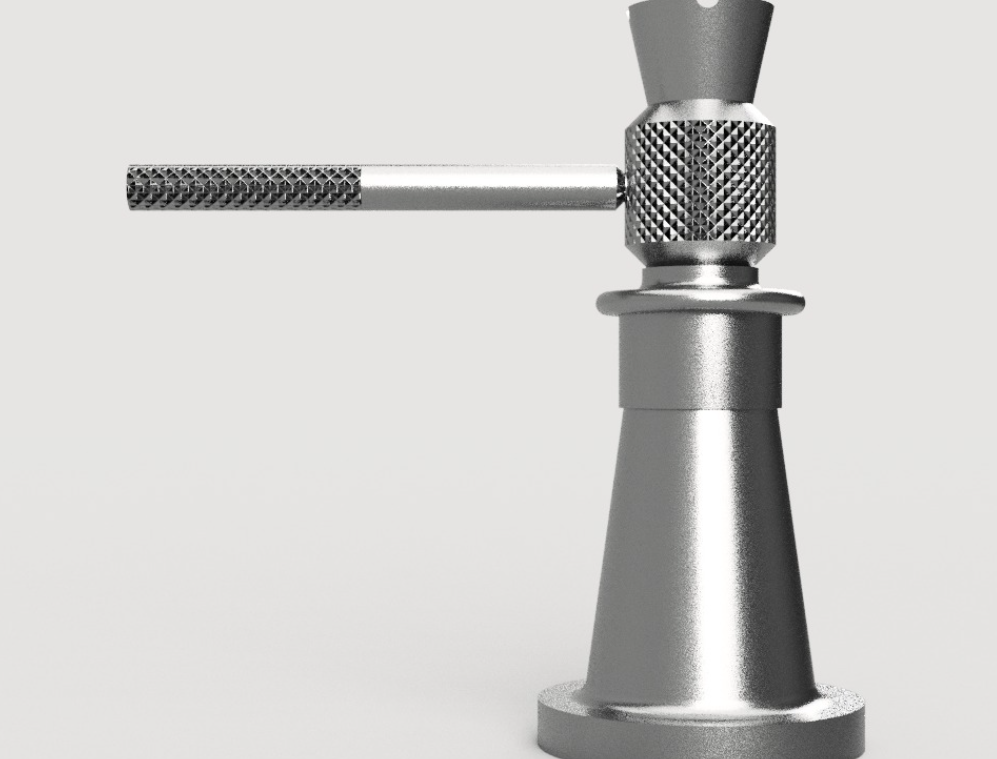
Screw jacks are used worldwide to lift, align, position and secure loads, making them an excellent solution for numerous applications. Their high reliability and synchronization make them the ideal solution.
To properly install and maintain a screw jack system, it is crucial that all necessary components are assembled and placed correctly – this will help ensure optimal performance, longevity and safety of your equipment.
A typical screw jack system consists of a gear housing, trapezoidal lifting screw (commonly known as lead screw), worm screw and worm gear system. The latter can either be manually or electrically rotated while the lead screw moves through it – with its linear motion speed dependent upon thread size and rotation ratio of its respective worm gears.